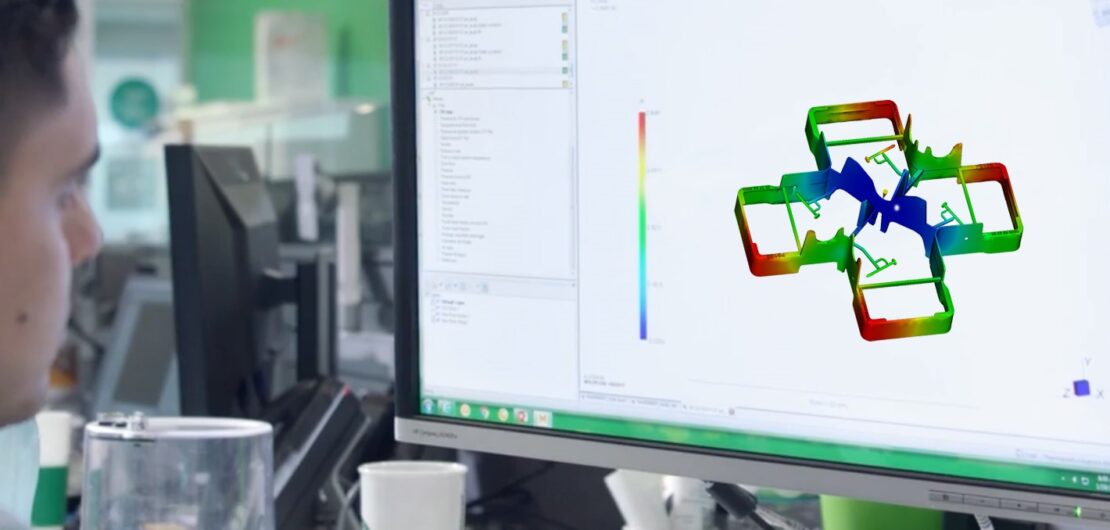
Product Design
Our CAD System
We use SolidWorks for all design work at NTD. SolidWorks is a world-leading software package ideal for the complex 3D design of injection moulded parts. We use SolidWorks to design parts and then use those models to design the complete mould tool assembly.
SolidWorks is an integral part of the manufacturing process and works seamlessly with our CAM (computer-aided machining) software – CamWorks – to produce toolpath code during the tool build phase.
In-House Tool Design
Tool design is a critical part of the manufacturing process. Designing the perfect tool for your product requires the consideration of many factors. Some key factors include:
- The production method
- The overall product
- Specifics about the product (shape, function, material)
- Process choice
- Surface treatment
- Packaging
- Assembly
- Delivery
Our tool design team work closely with tooling and prototyping to optimise the quality of your product while reducing manufacturing costs. Using Moldflow, FMEA and tolerance analyses, we can refine the design to ensure minimal delay between the first shots off the tool and mass production.
Rapid Prototyping
We use in-house 3D printing to help in the design of products and tools. Through a range of carefully selected partners, we can also access a variety of other printing technologies. These include FDM, SLS, SLA, DMLS and MJF. This is complemented by our wide range of materials and surface finishes to optimise design detail and product performance prior to cutting steel.
.
Product Analysis
.
Moldflow Analysis
Moldflow is rated as the number one plastics simulation software by injection moulding professionals worldwide. The software analyses and predicts how the plastic material will flow through the mould tool. It will produce results telling us fill time, pressure required to fill, temperature drop across the part, and sink and quality predictions. Moldflow also allows us to optimise part and mould design before cutting steel. Our analysis involves:
- Validation of part design and recommendation for improvement
- Polymer selection – evaluation of alternate polymers
- Balancing of feed system for family moulds
- Optimisation of process parameters
- Cooling analysis to check and improve cooling layouts
- Determination of part warpage and corrective measures to reduce warpage